American Plastic Molds are the core of injection molding. They are custom made to hold hot melted plastic, and they are a key component in the process.
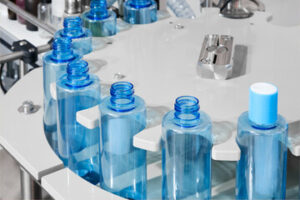
The process is relatively efficient, resulting in very little material waste. This is a great advantage over processes like CNC machining, which generate significant waste.
High volume injection molding is a production process that allows for large-scale manufacturing without sacrificing quality or efficiency. Its automated nature, advanced machinery, and precision molds allow for quick turnaround times that reduce production costs per unit. This makes it ideal for companies with high-demand product demands and tight production deadlines. Additionally, it is compatible with a variety of thermoplastic materials to suit functional and aesthetic requirements.
Achieving uniformity in the dimensions, appearance, and properties of plastic molded parts is crucial for maintaining brand consistency. This is particularly important for high-volume production, as even a single flaw in the final product can have major consequences. However, achieving consistent quality is a multifaceted endeavor that requires optimized processes and stringent quality control measures.
For this reason, it is critical to choose a plastic molding supplier with a proven track record and a commitment to ongoing customer satisfaction. Request examples of previous projects and read customer testimonials to gauge the manufacturer’s reputation for reliability. Additionally, look for factories that offer transparent pricing structures to avoid unexpected fees and expenses.
The process of high-volume injection molding begins with creating detailed designs and blueprints using CAD software. Next, the molded parts are designed and manufactured from high-grade materials like steel or aluminum for durability. When the design is ready to be produced, molten plastic is injected into the mold cavity under high pressure. After filling the entire cavity, it is cooled and solidified to form the final plastic part. A variety of quality checks are performed throughout the production cycle to ensure accuracy, strength, and durability.
Injection molding is a complex process, but one that offers many benefits for manufacturers of all sizes. The shortened production cycle reduces overall labor costs and lead time, while ensuring that each piece meets industry standards and customer expectations. In addition, the ability to produce a variety of parts with the same tooling and dimensional specifications reduces costs and enables businesses to respond quickly to changing market conditions.
Low Volume
Low volume plastic injection molding is ideal for businesses that require bespoke, custom plastic products in smaller quantities. It is a cost-efficient and fast alternative to traditional manufacturing, and can also be used for reoccurring low-volume production runs. Using low-volume injection molds allows manufacturers to keep a close eye on costs and ensure high-tolerance accuracy while still keeping their product on the market and able to meet demand.
Injection molding requires highly-engineered molds — known as “tooling.” These can be expensive to produce, especially for small-volume orders. But if you are able to commit to recurrent small-volume runs, the return on investment will be greater than if you need one or two of each product. For this reason, it is important to consider your long-term needs when considering a new project and how much volume you anticipate needing in the future.
The right materials are essential to the success of your low-volume injection mold. You will want to collaborate closely with your material suppliers and mold designers to ensure that the selected materials align with your specific project’s requirements and goals.
Different materials have unique properties that can make them the best choice for your particular project. For example, acrylic plastics are inexpensive and durable, but they do not offer the same level of rigidity as ABS or other engineering-grade thermoplastics. Acrylic can also be easily scratched or damaged, and its service temperature is too low for certain industrial applications.
When choosing a supplier for your low-volume injection molds, look for one that specializes in the process. Experienced providers understand the nuances of different processes and can advise you on the most efficient methods to use. They will work to meet your deadlines while still maintaining the highest quality standards.
A low-volume manufacturer should have the ability to quote in real-time and provide a self-service portal for customers. This will eliminate quoting delays and increase visibility throughout production. They will also be able to leverage advanced technology like Big Data analytics and Industry 4.0 integration to automate their workflows, improve efficiency and reduce error rates. This will help you get your products to market faster and will lower the risk of monetary loss if the project fails.
Repeated Shape
A plastic mold that has multiple cavities or a repeated shape is often used for injection molding. This type of mold allows for more flexibility and increased production efficiency. It also allows for the use of different materials and designs that might not be possible with a single-cavity mold.
Injection Molding is the process of converting raw material into a plastic product by inserting it into a pre-shaped cavity in a mold and then pressing it down under high pressure until it takes on the desired form. This method is used to produce a variety of products from phones to car parts and even medical devices. The advantage to this method is that it allows for less waste as the melted plastic is transferred evenly throughout the several cavities in the mold. It is also a very popular choice for producing hollowed out plastic products like bins and kayaks.
Core and cavity are the key components that define the shape, dimensions, and quality of a molded part. A well-designed core and cavity will ensure that the molten plastic is evenly distributed over all areas of the mold to create a consistent product. This will also provide better quality and precision of the finished product.
CURING TEMPERATURE – The temperature at which a plastic is placed in a mold to cure and change its physical properties. This usually occurs through a chemical reaction called condensation, polymerization, or vulcanization.
DRY COLORING – Method commonly used by fabricators for coloring plastic by tumble blending uncolored particles of the molding material with selected dyes and pigments. This is typically the fastest and least expensive way to color plastic.
EJECTOR PIN – A rod, pin or sleeve that pushes a molding off of a core or out of a cavity of a mold; attaches to the ejector bar or plate. This pin can be actuated by the ejector rod(s) of the press or by auxiliary hydraulic or air cylinders.
ELASTICITY – A property of some materials that allows them to stretch under low stress to at least twice their original length and then snap back to the original position upon release of the stress. This is especially important in a molding application where the molded product may be subject to a significant amount of stress.
Custom
If your company is in the business of manufacturing custom plastic pieces, it’s important to know how to optimize your manufacturing process. This will help you avoid paying excessive fees to independent sellers and make your products more attractive to your clients.
One of the most popular methods for achieving this is custom injection molding. This type of molding is a versatile method that can produce various shapes and sizes of products. It is also highly customizable, allowing you to add different additives and color finishes. In addition, it is ideal for creating precise molds that can be used in design projects and scientific experiments.
The first step in creating a custom mold is to use a computer-aided design software program to create a digital model of the desired product. This model can then be used to make a physical prototype using 3D printing or other rapid prototyping techniques. During this phase, it is crucial to pay attention to the dimensions of the final product. This will ensure that the plastic piece matches up with the design exactly.
Once the design is complete, the next step is to select a plastic material for the final product. This decision will be based on several factors, including the amount of production required, the cost of raw materials, and the strength of the finished product. It is also important to consider how the product will be handled and whether it needs to be able to withstand environmental conditions.
Finally, the plastic manufacturer will need to determine which molding technique is best for the project. This will depend on the size and shape of the finished product, as well as the number of features that will be integrated into the design. For example, if the part will be used to make a furniture item, the manufacturer may need to add ribs or gussets to increase its strength.
Using custom plastic molding to produce your products is a great way to save time and money in the long run. The process relies heavily on automation, which means that labor costs are lower than with other manufacturing processes. Additionally, high-volume production runs lead to significant savings in raw material costs due to economies of scale.