Plumber Woodland Hills are responsible for the installation, repair and maintenance of plumbing systems. These systems take away waste water, provide hot and cold water, and regulate indoor climate through pipes, valves and fixtures.
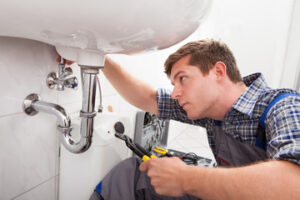
Plumbers need to have critical thinking skills in order to solve problems and come up with effective solutions. They also need physical strength and stamina to carry heavy loads and work in tight spaces.
A test-cock is a small valve used to draw water or air from a larger valve for testing purposes. It is typically found on backflow preventer assemblies as a way to test the pressure inside the device without having to take apart the entire thing.
Generally, a backflow preventer has two test-cocks: one on the inlet side of the device and one on the outlet side. The test-cocks can be opened and closed using a special tool (not included). We sell these handle-less valves that can easily be operated with an independent custom wrench. They are tamper resistant and work with Deringer or Magnum devices.
They are also commonly used as isolation valves for gauges and equipment lines. They are lead free and meet SDWA requirements.
Pressure Gauge
The pressure gauge is an important instrument in backflow testing. It helps determine whether the air ports and check valves are opening when they’re supposed to, preventing backflow of water or gases. It also tests the water taps and air hoses for pressure changes, which are often a sign of a faulty valve. Using the gauge, a technician can see whether the pressure is rising or falling. If it is rising, the valve will need to be replaced. If it is falling, the valve is functioning properly.
Pressure Gauges are self-contained indicators that convert detected pressure into mechanical motion of a pointer, which can be either analog or digital. They are used to monitor and display process pressure, and can be installed as part of the control system on a vessel, offshore rig or industrial plant. These instruments are widely used in chemical/petrochemical, power generation, oil & gas, mining and on/offshore applications. They are available in a variety of designs to suit different application requirements, and a number of factors like the operating pressure range, dial size, environment, accuracy, and medium type have to be taken into consideration.
Bourdon tube gauges are the most commonly used, and they are available in a wide range of sizes, types, and specifications to cater to various applications and industries. Their operating principle is based on the fact that a flattened, circular tube tends to straighten and re-gain its circular form in cross-section when pressurized (think party horn). The change in cross section is magnified by forming the tube into a C shape or even a helix, and this is what allows these devices to measure gauge pressure, which is relative to atmospheric pressure.
Other types of pressure gauges use other principles to measure pressure. Hydrostatic gauges (like the mercury column manometer) compare pressure to the hydrostatic force per unit area at the base of a column of fluid. Piston-type gauges counterbalance the pressure of a fluid with a spring or solid weight (for example, a tire or an air-pressure gauge of comparatively low accuracy). Piston-type pressure gauges have good dynamic response but are susceptible to leakage and calibration problems.
Gate Valve
The gate valve is a component of a backflow prevention system that protects pipes from backflow by blocking reverse flow. This prevents the introduction of pollutants and hazardous substances into your plumbing infrastructure. This device is essential to ensuring that your backflow testing system functions properly, and it’s important to understand its function in order to properly manage your water.
The structure of the gate valve is a straight, cylindrical or slightly tapered structure with threaded or flanged connections on either end. It serves as the housing for the valve components and the flow path for the fluid. It is operated by the valve handle or operating mechanism, which consists of a valve stem, a gate plate and the valve seat. The valve seat is the contact point between the gate and the valve disc, which allows or restricts the flow of fluid. The gate disc is a flat or wedge-shaped component attached to the valve seat, and it is raised or lowered by the valve stem using the operator’s hand wheel.
A gate valve has a long service life and is easy to maintain. It’s also an excellent choice for low pressure applications and has a lower operating torque than ball valves, allowing for easier operation. In addition, the resilient seal minimizes leakage and reduces wasted water. It also has a smooth flow path, which minimizes head loss and improves system efficiency.
There are several causes of gate valve failure. Sediment buildup can prevent the valve from closing fully, and corrosion can lead to a broken seal. In addition, the design and valve size can play a role in gate valve performance.
When a gate valve fails, it’s best to turn off the water supply and drain the pipe before performing repairs. It’s also a good idea to heat up the valve joints and stem with a torch before attempting to remove or replace the valve. You can then use channel locks to separate the valve body from the handle stem and seating. Once the valve is removed, it’s important to clean any atmospheric deposits from the valve stem threads and apply 3-in-one or penetrating oil before tightening the packing nut and screw.
Relief Valve
The Relief Valve or safety valve is the last line of defense to prevent catastrophic damage from a backflow event. It operates to discharge water prior to flow reversal, whether it is caused by backpressure or by backsiphonage, so that it is not trapped in the system. It is the one piece of equipment in a backflow assembly that is most likely to fail due to wear and tear, fluid or environmental conditions, and incorrect operation. A quality pressure relief valve can be designed from a wide variety of materials to handle different temperatures, chemical conditions, and applications. Brass, plastic, aluminum, and a wide range of grades of stainless steel are common choices.
Once the inlet shut off valve is opened and backflow testing is underway, plumbers hook up test hoses to open and close gate and relief valves on their tester. They also read the gauges on their tester to determine if there are any areas with low pressure or air ports that are not opening as they should.
The #1 Check valve is responsible for preventing backflow, but as the pressure in the system increases it will push past the #1 check and increase Zone pressure until it reaches the pressure of the #2 check seat (for example 98 PSI) or the relief valve opening point (2 PSID). As this happens, the #1 Check Valve will become more compressed with a higher disc compression, causing the Relief Valve to open and allow the high pressure water to flow out through the bleeder port into the end-user’s plumbing.
Conventional spring loaded pressure relief valves use a disc that rests on the valve seat until pressure reaches a threshold where it is overcome by the spring tension, lifting the disc to open the valve. Modern versions of this type of valve, known as Bellows Assisted Pressure Relief Valves, feature a mechanism that balances the impact of system pressure on the disc to ensure it only opens when there is an actual increase in system pressure not just back pressure.
If the Relief Valve is not opening at the required minimum pressure, it could be caused by a variety of factors such as debris lodged between the #2 Check valve seat and sealing disc or the components are damaged. The other cause of a low Relief Valve opening point is an obstruction in the Relief Valve stem mechanism such as a restriction in the guide or corrosion which causes the relief valve stem to not travel optimally leading to a lower pressure point than desired.